Work procedures

The advantage of a template is that you always know where to look to find the information you're after, even though the details differ from one example to another.
Below is a summary of the main types of documented work procedures you're likely to use in the floor covering industry.
You'll find more information on the various safe work procedures in the unit: Safety at work.


Cutting list
Cutting lists can be laid out in lots of different ways, depending on the material you're cutting and the task you're doing.
For example, if you were cutting skirting boards or trimming sheets, you may list the different lengths that need to be cut and the number of pieces required at each length.


'Recovery' refers to the amount of good pieces you are able to cut from a roll, with the minimum amount of waste, by working the measurements you need into the roll lengths available.


SOP
The purpose of a safe operating procedure (SOP) is to describe how to use a machine or carry out the task safely and in accordance with the company's policies and manufacturer's guidelines.
The sample SOP linked below has a typical layout, with an activity description that defines the task, a list of potential hazards and safety controls, a set of pre-start checks, and a brief operational procedure.


SWMS
A safe work method statement (SWMS) is a formal document that lists all the tasks involved in completing a job and describes how the hazards will be controlled.
On building sites they are mandatory for 'high risk construction work'.
However, on some sites all contractors are asked to complete a SWMS before they start work - including flooring installers.


MSDS
A material safety data sheet (MSDS) - also called a safety data sheet (SDS) - is a summary of the safety procedures you should follow when using or handling a hazardous product, and the main health issues relating to it.
There are some variations in layout between different manufacturers' MSDS, but they all have the same sorts of subheadings.
The example linked below shows the first 2 pages of a 14 page MSDS for Ardex K15 levelling compound.

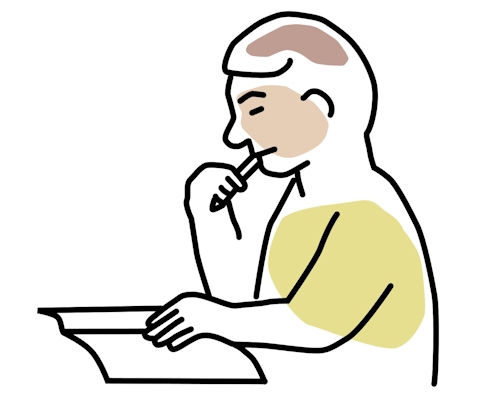
Learning activity
Audio 8 (mp3 |6|KB)We've discussed SOPs, MSDSs and SWMSs in other units in the Flooring Technology resource. But we haven't talked specifically about cutting lists elsewhere.
Do you use cutting lists for any products? For example, you might use them to pre-cut inlay pieces or pre-formed coving.
Or on larger jobs you might use them to cut rolls of material to a range of different lengths.
Describe the situations where you have used a cutting list and what it looked like.

